Production Planner
Tasks & duties
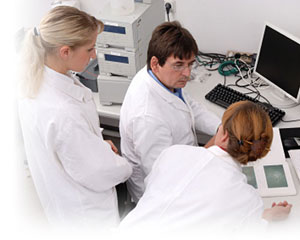
Production planners may do some or all of the following:
-
calculate the amount and type of materials needed for production
-
prepare schedules stating when materials are required
-
arrange the purchasing and delivery of materials for production
-
maintain stock of materials
-
prepare timetables for production
-
change the production schedule when necessary
-
write reports and keep records on production progress
-
ensure production deadlines are met
-
complete office administration duties
-
trial new production equipment
Skills & knowledge
Production planners need to have:
-
knowledge of production processes and materials
-
analytical skills to interpret figures and information
-
people skills including the ability to manage and lead people
-
computer skills
-
time management and planning skills
-
maths and problem-solving skills
-
good communication skills
They may also need to have specialist technical knowledge depending on the requirements of their role.
Entry requirements
There are no specific entry requirements to become a production planner. However, a Diploma in Purchasing and Materials Management is useful. Production planners can gain certification through the
New Zealand Production and Inventory Control Society (NZPICS), which offers modules in all aspects of production planning, such as supply chain management.
Tertiary education
A technical background, such as in science or engineering, may be required for some planning roles that have a technical component.
Training on the job
Skills are gained on the job. Some production planners may complete training courses to learn computer and management skills.
Useful experience
Useful experience for production planners includes:
-
office work
-
factory work
-
work involving buying and selling
Related courses
Manufacturing Engineering
Project Management
Quality Management
For more information, please refer to Career Services.
Document Actions